ピッキングソリューション
最短時間で誤品率0(ゼロ) に挑む。
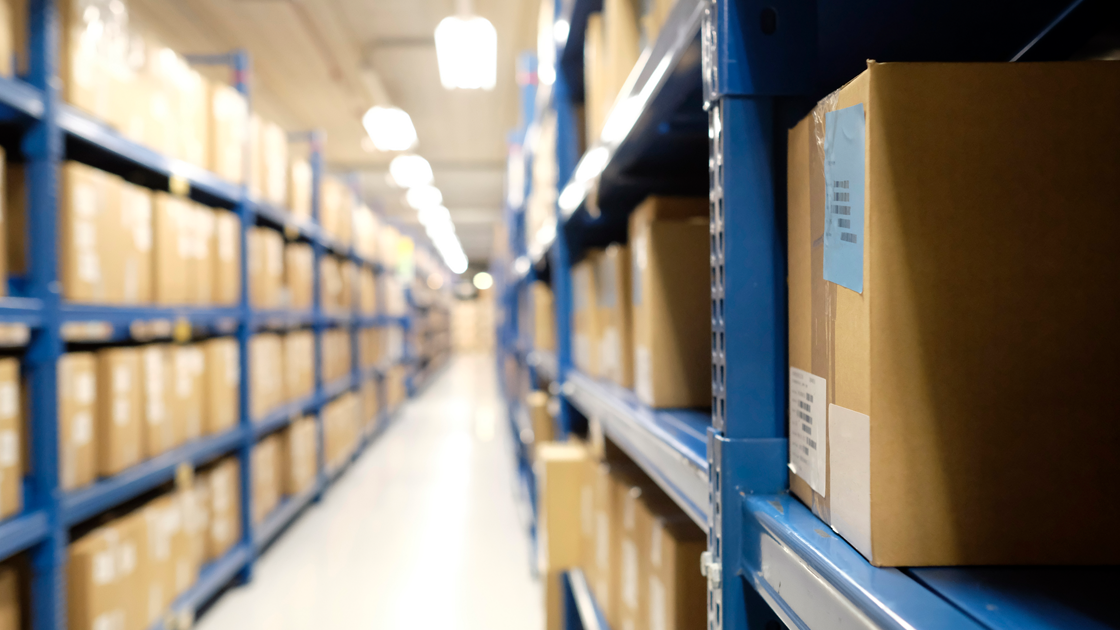
ソリューション概要
ピッキングの作業精度と生産性アップ。独自のアルゴリズムで動線最適化を実現。
入出庫管理システム (IT-MatexIII) からのリアルタイムな指示により最短経路でピッキング。しかも、計量器付きAIピッキングカートが数量検品を同時処理。誤品率を低減しながら作業者の負担を大幅に軽減します。
このソリューションで解決できる課題
詳細
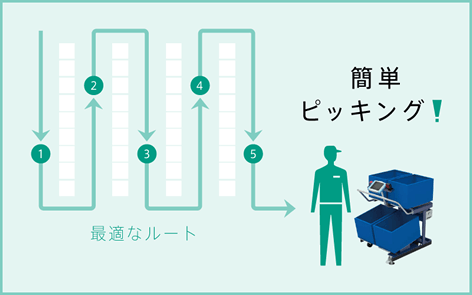
作業動線最適化と渋滞回避
作業指示データに基づき、TERAOKAが独自に開発した動線短縮のアルゴリズムが最適なルートでのピッキング作業に誘導。無駄な移動時間をなくします。並行して特定通路の渋滞を予測し、待機時間のロスを未然に防ぎます。
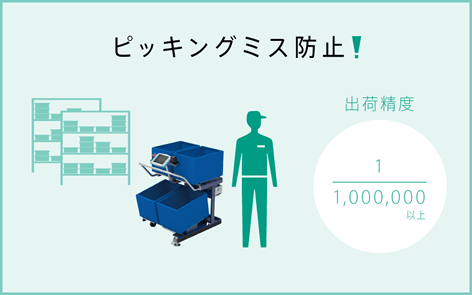
ピッキングと同時に数量検出
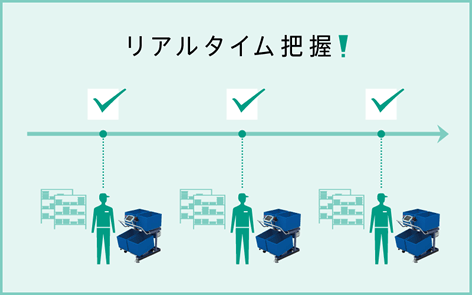
生産性管理
リアルタイムに収集した実績により、カートの稼動状況や作業者別進捗などの把握が簡単にできます。ペーパーレスでの履歴分析は、コスト削減と同時に生産性アップに貢献します。
導入事例
「AIピッキングカート」と「SPK」の導入で作業効率が大幅アップ、生産性も向上
東京ロジファクトリー株式会社
東京・神奈川・埼玉で物流展開を行っている東京ロジファクトリー株式会社。
今回、新しい出荷業務に伴い、作業効率と生産性向上のために「AIピッキングカート」と「SPK」を導入しました。
出荷時の検品・詰め替え作業が不要になりました
ピッキング時に、カート本体から適切な段ボール箱のサイズが指示され、それをカートに載せて作業することで、出荷時の検品・詰め替え作業が不要になりました。事前に「SPK」で商品の長さ・幅・高さを計測して、商品を撮影した“商品マスター”を作成しているので、「AIピッキングカート」でのピッキング時には、商品マスターと照合し、そのまま検品レスで商品を出荷することができます。
「AIピッキングカート」、「SPK」の導入で、ピッキング時の二重 (スキャン&重量) 検品による精度向上、梱包時の検品作業削減による生産性向上を実現
ケイヒン配送株式会社
ケイヒン配送株式会社は、40年以上にわたり、少量多品種の商品を取り扱う物流業務に携わってきました。当初は主に大手百貨店の物流センター作業と宅配業務を、現在は通信販売会社や小売業者の物流業務受託に注力しています。
今回、化粧品や雑貨などを扱うお客様から委託されているエリアの出荷精度を高めるため、「AIピッキングカート (重量検品カート)」と「高精度採寸計量スケール SPK」を導入しました。
ピッキングと検品を同時に行えることで、精度の高いサービスを実現
『SPK』で重さと容積を計測して商品マスタを作り、そのデータを『AIピッキングカート』に取り込む仕組みを使うことで、ピッキングと検品を同時に行うことができるようになりました。その結果、検品がなくなり、さらに梱包作業場所の削減にもなりました。
スタッフの作業効率がアップ
『AIピッキングカート』と『SPK』の導入前は、作業効率が個人の経験値に依存してしまうなどの課題がありましたが、導入後はこれらが驚くほど改善されました。ピッキング時、モニターに商品マスタが表示されるので、どの商品をピッキングするか視覚的に確認することができます。そのおかげで作業効率が平準化され、向上していると感じています。
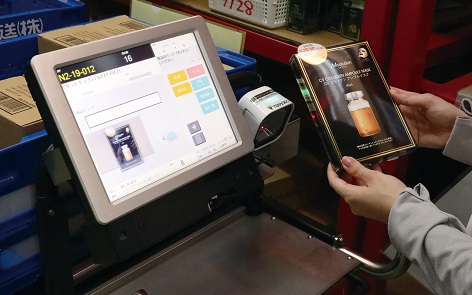
ピッキング作業の精度が上がって、効率が劇的によくなりました。
株式会社あらた つくば物流センター様
AI (人口知能) による作業動線の最適化
オーダー内容から最適なピッキングルートを算出する渋滞回避アルゴリズムにより、ピッキング時の移動距離が減って無駄のない作業ができるようになりました。
正確なマルチピッキング
内蔵されたはかりにより数量を正確に検出できますので、4オーダーの並行作業でも個数を間違うことがなく安心です。